Busbars are essential components in the electrical systems of electric vehicles (EVs), serving as conductive pathways that distribute power from the battery to various components, including the electric motor and onboard electronics. Given their critical role in ensuring efficiency and safety, accurate inspection of busbar dimensions is crucial in EV manufacturing. Here’s our guide on effective inspection of busbar dimensions with a focus on electric vehicles.
Understanding busbars in Electric Vehicles
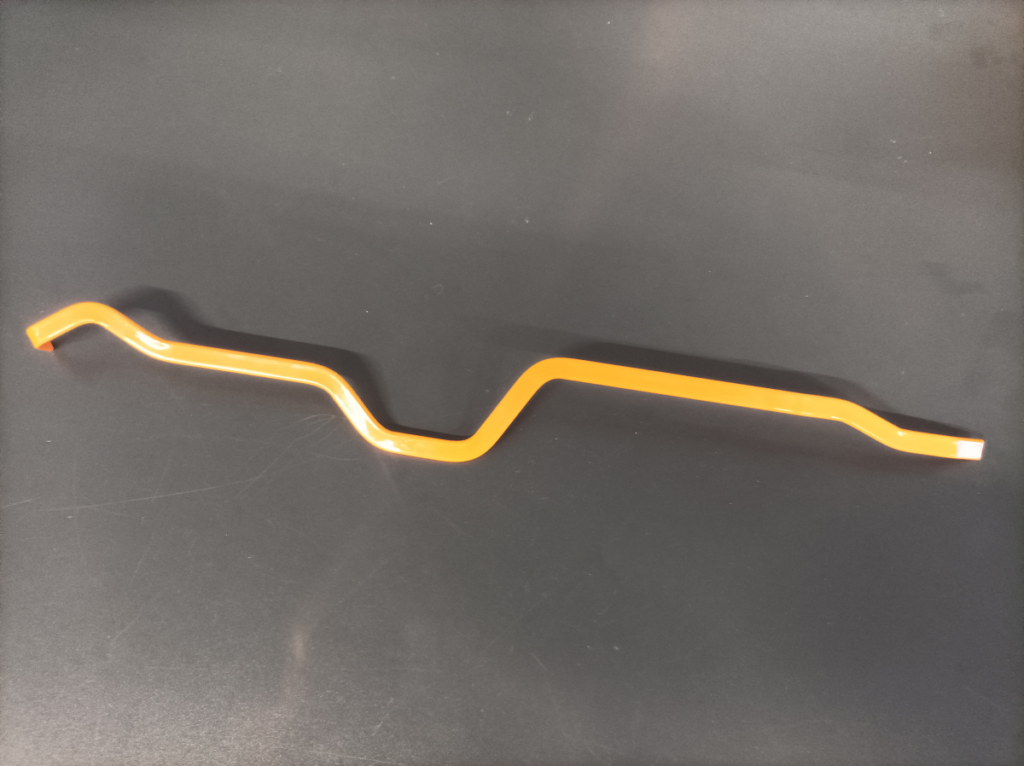
Busbars in electric vehicles are typically made of copper or aluminum and come in various shapes and sizes. Some have rectangular cross-sections and run just a few inches, while others use circular cross-sections and run nearly the length of the vehicle. They are designed to manage the high currents generated by EV batteries and must withstand significant thermal and mechanical stresses. Due to the tight space constraints of battery packaging and electrical distribution inside the vehicle, busbars are bent and twisted to specific shapes tailored to meet particular requirements. Ensuring the correct size and shape of busbars is vital for optimal performance and safety in EV applications.
Key Dimensions to Inspect
When inspecting busbars for electric vehicles, several key dimensions must be validated:
- Width: The width of the busbar affects its current-carrying capacity, which is critical for handling the power demands of an electric vehicle. This dimension is easily controlled by incoming material.
- Thickness: Thicker busbars can handle higher currents but may add weight, impacting vehicle efficiency. Thickness is also controlled primarily via incoming material.
- Length: The overall length must match design specifications to meet electrical requirements and ensure proper fit within the EV’s. Confirming proper length after forming is an essential requirement.
- Bend and Twist Angles: The bends and twists are the main factors that determine the final busbar shape and dictate whether they will properly fit without potentially dangerous interference or rubbing. These essential characteristics must be checked as part of the overall form.
- Hole Position: Since busbars conduct current from point A to point B, they often have connector holes at the ends or sometimes in the middle. These holes must be located correctly to enable the termination of electrical connections.
Inspection Techniques
There are several methods manufacturers can utilize for inspecting busbar dimensions specifically for electric vehicles:
1. Manual Measurement
Calipers, micrometers, height gauges, and inclinometers can be used to measure the key dimensions mentioned above. However, these methods can be time-consuming and often exhibit operator-to-operator variation in measurements.
2. Gauges
Hard gauges can be used to check go/no go fit of formed busbars. While fast and easy, they provide no variable data for process control nor do they give feedback about what to fix if the busbar fails. Gauges are also susceptible to eager operators who may apply a little extra force to make a non-conforming part fit into the gauge.
3. Coordinate Measuring Machines (CMM)
CMMs offer high precision by using a probe to touch various points on the busbar and collect data. However, formed busbars, tubes and wires are notoriously challenging to measure using CMM. Such parts are difficult to fixture and align so the process can be cumbersome and slow so is rarely used for such parts.
4. 3D Scanner
3D scanners using lasers or structural light may be used to dimensionally inspect many different kinds of parts, including busbars. This approach may be a viable option if the quality lab already has a scanner. Still, there are a couple of limitations that prevent the scanner from being an ideal solution. The first is that busbars often have translucent and/or reflective coatings, making it challenging for many 3D scanners to acquire good scan data from the surface. Acquiring a good point cloud may require either making many adjustments to scanning parameters or the use of scanning spray to dull the surface. Secondly, if good scan data is acquired, general inspection software can quickly inspect and identify whether the busbar shape is in tolerance. However, if it is out of tolerance, there is no feedback to indicate what adjustments to make to achieve in tolerance condition.
5. Optical Measurement Systems
Optical measurement technologies like the 3D Hairpin Inspect and TubeInspect systems have emerged as game-changers when inspecting busbar dimensions for electric vehicles. These systems use non-contact, photogrammetry-based methods to capture busbar dimensions quickly and accurately.
- Speed: Optical systems measure the full 3D busbar shape and inspect critical dimensions in seconds, significantly reducing inspection time in fast-paced EV manufacturing environments.
- Accuracy: By instantly measuring the actual shape with an accuracy of 0.035mm and comparing it directly to CAD-based nominal data, this technology immediately identifies any deviations, ensuring that each busbar meets stringent quality standards.
- Ease of Use: There is no reliance upon a skilled technician to perform the inspection. The operator merely places the busbar in the inspection system and pushes a button. The inspection is automatic.
- No Fixturing Required: Unlike many traditional methods, these optical systems do not require fixtures or holding devices, making them highly flexible for various shapes and sizes.
The Advantages of Optical Measurement Systems
Optical measurement provides several advantages over conventional inspection methods that we should consider for our electric vehicle applications:
- Instant Results: We receive immediate feedback on whether the busbar meets specifications, allowing us to maintain a high sample rate and make quick adjustments if necessary.
- Identify Corrections: When deviations are detected, the system can automatically suggest adjustments to the manufacturing process to achieve in-tolerance parts, thereby reducing waste.
- Increased Productivity: Faster inspections and calculated corrections lead to quicker setups and changes between different parts, optimizing your production efficiency in the competitive EV market.
- Flexibility: A single optical gauge can be programmed to inspect thousands of different busbar shapes if needed without any additional equipment or fixturing.
Driving Quality Assurance Forward
At Accurex, we understand that pushing the boundaries of electric vehicle technology hinges on the reliability of every component. That’s why precise inspection of busbar dimensions is crucial—not only for enhancing performance but also for ensuring the overall safety and efficiency of your electric vehicles.
By integrating TUBEINSPECT and 3D Hairpin Inspect into your quality control processes, you can improve efficiency, reduce costs, and foster innovation in your electric vehicle production. This solution positions your operations at the forefront of the EV industry, enabling you to meet the increasing demands for safety and performance in electric mobility. Contact Accurex today to learn more.