The Importance of Aircraft Fasteners
At Accurex Measurement, we specialize in niche optical measurement and inspection applications that are often “hidden in plain sight” from the average person.
For example, consider the fasteners used to assemble aircraft. “Fasteners?,” you say, “What are you talking about?” That is exactly the point. In 2023, US airline carriers flew over one trillion revenue passenger miles for passenger flights (per US Dept. of Transportation, Bureau of Transportation Statistics. ) That is a lot of people spending a lot of time on airplanes. Yet we can confidently say that most of those passengers had exactly zero thoughts about aircraft fasteners. However, the companies and people who manufacture those aircraft and their many subassemblies invested a lot of time and effort to ensure that the fasteners were correct and would do their jobs perfectly.

Challenges Faced by Airline Manufacturers
Modern aircraft assembly relies on many thousands of fasteners of all types and sizes. All have vital roles, but some are more critical than others. Aircraft fasteners are installed according to strict requirements that exist for many reasons such as:
Structural – Fasteners that are installed too deep, or at an improper angle can affect the structural integrity of the assembly.
Performance – Fasteners that are too high (a.k.a. “proud”) can fail aero smoothness requirements and cause excess drag, which affects the aircraft’s all-important efficiency.
Special needs – Some aircraft are designed for particular conditions that require low/no radar signature, or they travel at extremely high speeds where a slight surface disturbance can have unpleasant consequences.
Manufacturers are tasked with inspecting the fastener flushness to ensure that installed fasteners meet their requirements. This is the quality requirement. They are also challenged to do so efficiently – with speed, precision, and reliability – because these same manufacturers need to meet the increasing demand for their products. This is the production demand. The trouble for manufacturers is that these two needs are seemingly at odds.
Solution: FMT3 – Fastener Measurement Tool
Fear not – we have good news! There is a single solution for both challenges: FMT3 – the Fastener Measurement Tool, available from Accurex Measurement.
Features of FMT3
FMT3 is a handheld, high fidelity, multiline, laser scanner developed for aerospace fastener inspections. FMT3 is actually three solutions in one, with three available measurement modes:
- Fastener flushness – measure the height of the fastener head compared with the surrounding surface (outer mold line)
- Countersink – measure the characteristics of the countersunk hole (OML diameter, axis, countersink angle) and predict whether an installed fastener will be within specifications for flushness
- Filled Fastener/Surface defect – Detect and measure anomalies on an aircraft surface. Originally developed to inspect “filled fasteners” for low observable aircraft, this mode also enables inspection of high and low points for minor dents and dings.
Traditional measurements of these features involved the use of various tactile gauges that require skill and patience. Measuring these important characteristics with FMT is fast and easy – just pull the trigger on the handheld device.
FMT collects 3D point cloud data, automatically runs specialized algorithms to extract the desired measurements and displays results on the screen for user. Results are also saved on the FMT for later transfer for reporting purposes. FMT achieves measurement accuracy of 0.0003” for fastener flushness.
Using the FMT enables aircraft and aerostructure manufacturers to ensure proper drilling and installation of their fasteners quickly and efficiently. As a result, the rest of us can fly in comfort and confidence without a thought about the fasteners holding the flying machine together!
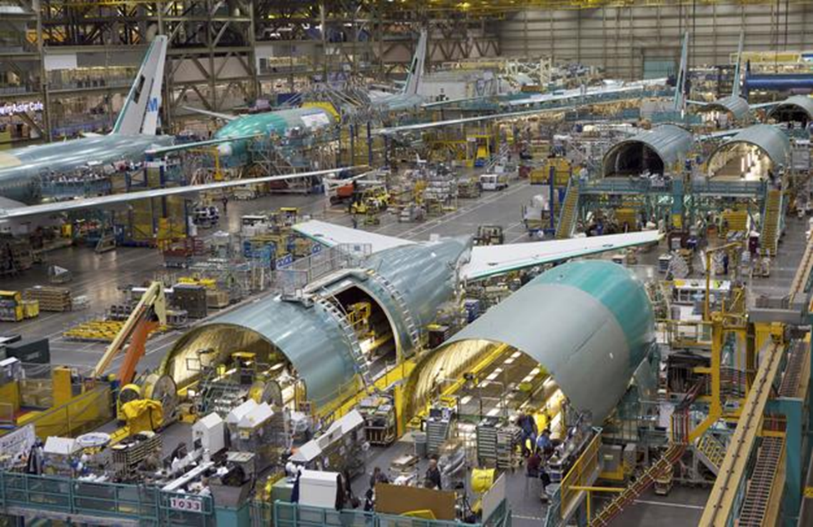
Can FMT help you with your fastener inspection? Learn more here https://accurexmeasure.com/fastener-inspection/ or drop us a note at info@accurexmeasure.com