A Brief History of Tube Bending Measurement
As long as manufacturers have been producing formed tubes, they have been wrestling with assessing and validating whether the bent tubes are the correct shape. This article will explain how BendingStudio’s method of measuring tubes and wires fundamentally differs from traditional methods and why it is a superior solution to support modern manufacturers of tubes, wire forms, and tubular assemblies.
A Brief History of Tube Gauging
Here is a tongue-in-cheek summary of the progression of tube gauging. While it is presented as a chronological progression, none of these methods have gone away. All are still used in some manner. Manufacturers select gauging methods based on a myriad of factors, sometimes with very analytical decisions and often from happenstance or tradition.
The Original Way
Bend a tube using whatever method is available. Try it where you intend to use it, and if it fits, great. If not, try again!
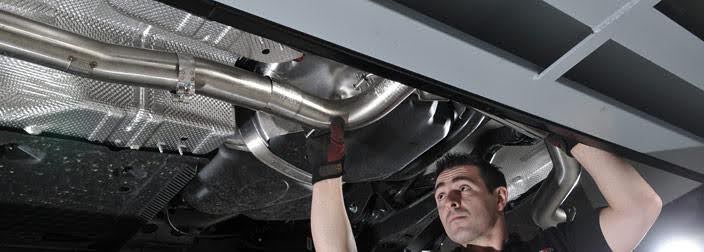
Tube Gauging 2.0
After a few frustrating trips on the trial-and-error treadmill, manufacturers decided they could create a simulation of the product’s eventual use. This led to the use of layouts and gauges. Layouts tend to utilize full-size prints, and often, height gauges are set up to represent the desired tube shape. A bent tube is placed over the print resting on the height blocks. Someone takes a look from different directions to see how everything lines up.
Gauges (also known as checking fixtures) require more commitment, where someone builds up a permanent fixture with appropriately positioned rests and blocks with guides representing tolerances. Some are pretty simple, and others are very elaborately machined full contour gauges. An inspector places a tube in the gauge to see if it goes in and fits within the checking points at the required locations.
If the part fits, great. If it does not fit well enough, then someone competent and usually quite experienced interprets the lack of fit and translates that observation into adjustments of the Length-Rotation-Angle (LRA) machine control parameters on the bender. Make the changes, bend another part, and repeat. You can start producing good parts when you get one that fits in the gauge.
Tube Gauging 3.0
In the early 1970s, an intelligent guy named Homer Eaton, who manufactured tube benders, recognized the challenge of the Original and Old ways and came up with a new idea. He invented the articulated arm to measure tubes and called it the Vector arm. This became a popular tool for tube measurement.
This particular method of tube measurement utilizes data only from the straight sections of the tube to construct the tube geometry. It initially used a couple of points from a touch or noncontact probe at the start and end of every straight section. It evolved over time to utilize laser scan data. But regardless of the source data, the technique constructs a series of cylinders.
Those cylinders are extended to the intersection, and the bends are assumed to be perfect with a nominal bend radius. This “intersection of straights” approach for tube measurement is really a reconstruction based on partial data.
When so much of the tube measurement is based on assumption, the LRA results from such methods tend to align reasonably well with the theoretical LRA model of the tube on which the assumptions are based. However, such methods have higher measurement uncertainty and are also susceptible to variation based on operator and tube conditions. This is why three people measuring a tube with this method will often get three different answers. The weaknesses of this method are minimized for relatively simple tubes with substantial bends and plenty of straight between bends. However, the limitation of the intersection of straights method is most pronounced for tubes with shallow bends, deep bends, and parts with short or no straight between bends. Unfortunately, those are the types of tubes that are more difficult to produce well and are where inspection is critical.
Tube Gauging 4.0
In the early 1990’s, a couple smart Ph.D students in Germany were challenged by their sponsor, an automobile manufacturer, with the task of finding a better way to measure automotive brake line tubes. They invented the TubeInspect system, which uses a series of photographs and the principles of photogrammetry to measure tubes. That underlying technology evolved into the pinnacle of tube bending measurement, the state of the art BendingStudio software. Measuring a tube with BendingStudio software using a TubeInspect or Absolute Arm laser scanner does not rely on the “intersection of straights” assumptions of older methods. BendingStudio uses data along the entire length of the tube – including data in the bends and straight sections – to determine its true shape. Rather than assuming tangent point locations, BendingStudio looks at where the tube begins to transition from straight to bend. The software uses advanced calculations based on a complete data set to calculate the tube characteristics, including centerline shape, tangent points, intersection points, rotation, and bend angles.
Because BendingStudio with TubeInspect and Absolute Arm scanner are measuring the tube with a more complete data set without assumptions, the resulting measurement of the actual tube geometry is more accurate, consistent, and ultimately more useful than other methods. When BendingStudio assesses a tube as within specifications, that determination is very reliable. When inspection from BendingStudio shows that a part is out of tolerance, the software calculates what corrections are necessary to produce a tube close to nominal, and those corrections are very effective, more so than from any other method of measurement.
Manufacturers involved with tube bending and the production of wire forms have multiple methods available to evaluate the dimensional conformance of their products. Each method of tube bending measurement has its own benefits and trade-offs in terms of cost, speed, and measurement performance. For manufacturers where reliable measurement, effective corrections and productivity are high priority, measuring tubes with BendingStudio and TubeInspect or Absolute Arm laser scanner is an excellent business decision.